精益生产的理论与实践
大中小本文对精益生产的起源、精益思维、精益生产在制造业企业的应用和效益做一讨论,最后澄清几个概念。 一、大规模定制 大规模定制(MC--MassCustomization)是1992年由约瑟夫.派因在《大规模定制--商业竞争的新前沿》一书中提出来的。大规模定制模式是指对定制的产品和服务进行个别的大规模生产。它不同于大量生产,也不同于多品种定制生产,而是两者相结合。大规模定制是企业经营中新的必然趋势,它能在不牺牲企业经济效益的前提下,了解并满足单个客户的需求。实现大规模定制的关键能力是:客户需求的采集,按20/80原则进行分析,产品设计必须标准化、模块化、系列化,生产工艺装备、生产流程的柔性化。工装模具的标准化,敏捷供应链的支持,信息系统的支持。大规模定制对信息系统的要求:物料清单的维护---可编号的物料清单,配置的物料清单,配置控制。生产过程同步化---严格的排产顺序,随车的配置清单,精确的领送料计划。 二、精益生产的应用。实现精益生产的目标,有大量的工作要做。图二是精益生产的目标体系 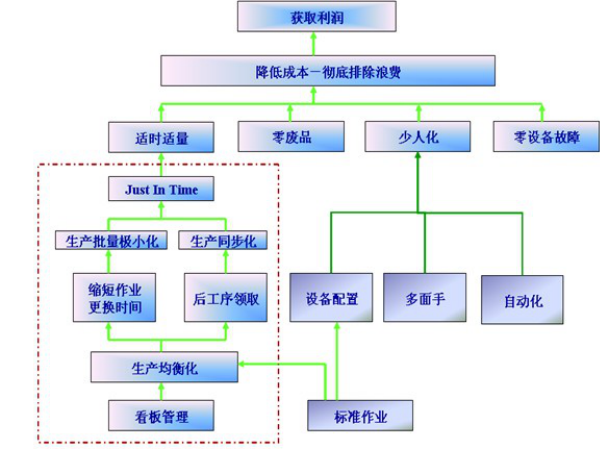
图二精益生产的目标体系 实现精益生产有许多事要做:企业要获取利润,必须降低成本,彻底消除浪费。采取的手段有实施适量生产即准时生产JIT,看板管理,全面生产维护TPM,5S管理,全面质量管理TQM,生产线的平衡,一个流生产,快速换模,缩短辅助时间等手段。下面我们对准时生产JIT和一个流生产的信息化解决方案进行简要介绍。 准时生产JIT(justintime) 准时生产的核心是为企业建立一整套供应链计划。有人误认为准时生产就是看板管理,只要有了看板卡,用看板卡从后序一级一级向前序领取或配送物料就万事大吉了。有的专门从事精益生产咨询的公司,他们排斥用信息系统,这是错误的。当今标准产品大批量生产的时代已经一去不复返了,大规模定制是主流,假设产品70%-80%的零部件是标准的,但是有20%-30%的零部件是可选的。产品配置的变化,使得零部件供应商不能按储备组织生产,而任何零部件的生产都是有提前期的,不是随要随有的。有些零部件的生产由于受到机床装备和工装模具的限制,只能组织批量轮番生产,这一切使得整个供应链的管理、物料的配送非常复杂,这就要求有一套快速响应客户需求的供应链计划系统。这个系统统筹考虑客户需求、产品配置,将中长期计划和短期计划相结合,将批量生产、准时生产和供应相结合。RS10准时生产供应链计划系统如图三所示。 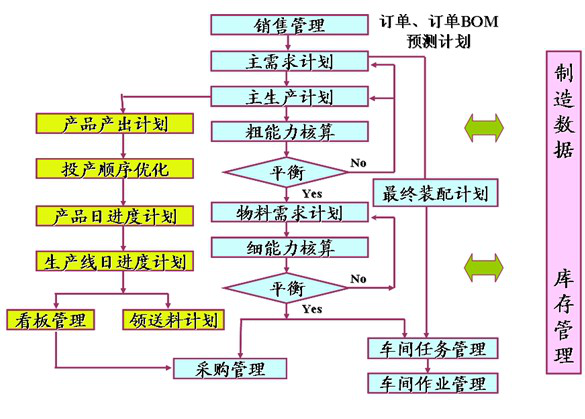
图三准时生产供应链计划系统 图三告诉我们通过销售系统将客户订单和预测需求生成主需求计划,考虑库存、在制和企业生产能力生成主生产计划,经过粗能力平衡验证主生产计划的可行性,上述两个计划是长期计划。物料需求计划将产品的需求通过物料清单、库存、在制、在途计算出什么时候需要什么物料,为供应和生产部门提供中期计划。他不仅回答了批量生产的生产计划,同时对准时配送的物料做了中期的预排产。然后对于批量生产车间通过车间任务管理、车间作业计划、车间统计实施生产制造管理。 对于流水生产车间先对总装线编制产品出产进度计划,投产顺序优化,再对部装流水线、零件生产线按反工艺方向安排每条生产线的日进度计划。 准时生产系统具有如下特点: 按每天或某时间段的计划量组织生产,而不是按离散的加工批量(Batch)、任务(JOB)组织生产。 采用拉式计划模式(PullSystem),按生产节拍计算每条生产线的投入产出时间。 采用倒冲法(Backflush)进行在制管理。 通过设置检测点(Checkpoint)进行数据收集和进度反馈。 跟踪物料到工位,提供按生产线上工位统计废品。 完整的供应链计划是一个批量生产和流水生产的混合模式。 支持看板管理,可按照每条生产线的生产计划生成供应看板和生产看板,支持电子供应。 需要注意的是,不能将精益生产、准时生产等同起来。精益生产集中于生产过程的整体优化--包括改进技术、理顺物流、杜绝超量生产、消除无效劳动和浪费、有效利用资源、降低成本、改善质量,达到以最少的投入实现****产出的目的。它是包括经营理念、管理、生产组织、生产计划与控制、作业管理、人员管理在内的一整套理论与方法体系。准时生产侧重于消除一切浪费的生产计划与控制的一整套方法。因此精益生产大于准时生产。 一个流生产 为了减少在制品,缩短提前期,减少中间质量检查,减少中间物料搬运,减少工人数,并大大提高工作效率,在设备允许的条件下,建议组建一个流的生产线,实现一个工人操作多台机床。如图四所示: 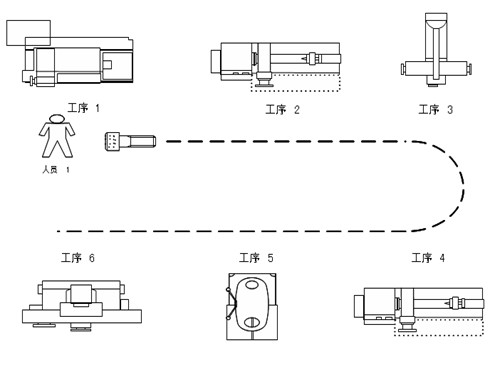
图四一个流生产 图中一个工人同时操作6台机床,加工某种零件的6道工序,他对6道工序的质量负责,中间无需质量检验。大大提高了效率,降低了成本。图五是批量生产与一个流生产效率的比较。 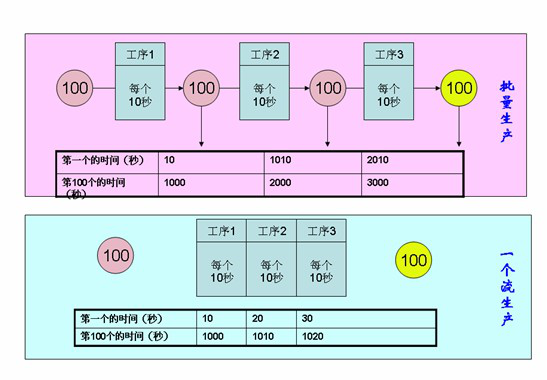
图五批量生产与一个流生产的比较 自工业革命以来,工业企业的生产组织方式经历了单件生产组织方式、大量生产组织方式与精益生产组织方式的发展历程。非精益的单件或大量生产组织方式中,都存在着大量浪费或不增值的活动,比如说生产过剩、零件不必要的移动与存放、操作工多余的动作、生产待工、质量不合格、从材料到产品的库存等等。而精益生产方式是当今世界公认的最具竞争力的先进生产组织方式,它是以永无止境的追求精益求精的过程,以尽善尽美为最终目标,充分发挥人的潜力致力于持续改进生产流程和流程中的每一道工序,从而提高劳动利用率,尽****可能消除价值链中一切不能增加价值的活动的生产组织方式。精益生产方式区别于传统的生产管理组织方式主要有:拉动式准时化生产、全面质量管理、团队工作法以及并行工程。 企业凝聚力和责任心的缺乏也是“精益”难以推行的重要原因。在丰田公司生产现场,可以做到没有一个专职质检员,而将产品质量保证到位,因为他们人人都是质量检验员。在中国,企业在检验环节投入了大量人力物力,却仍有大量错检、漏检,其质量损失比精益生产方式下无专职检验的企业要高得多。 精益生产方式下,人人都是“改善”的主体,只有源自内心的,以真正“主人翁”的心态工作与思考才能不断将“改善”有效推行,才能将精益生产方式真正落到实处。而当前,中国企业多数以处罚为主的“强势”下压的管理方式,是很难调动与激发多数员工的“主人翁”意识,从而很难用心去“改善”,更不用说全面精益生产了。 精益生产理论知识(二)
一、起源: 精益生产(Lean Production,简称LP)是美国麻省理工学院数位国际汽车计划组织(IMVP)的专家对日本丰田准时化生产JIT(Just In Time)生产方式的赞誉称呼。精益生产方式源于丰田生产方式,是由美国麻省理工学院组织世界上17个国家的专家、学者,花费5年时间,耗资500万美元,以汽车工业这一开创大批量生产方式和精益生产方式JIT的典型工业为例,经理论化后总结出来的。精益生产方式的优越性不仅体现在生产制造系统,同样也体现在产品开发、协作配套、营销网络以及经营管理等各个方面,它是当前工业界****的一种生产组织体系和方式,也必将成为二十一世纪标准的全球生产体系。 精益生产方式是战后日本汽车工业遭到的“资源稀缺”和“多品种、少批量”的市场制约的产物。它是从丰田相佐诘开始,经丰田喜一郎及大野耐一等人的共同努力,直到20世纪60年代才逐步完善而形成的。 产生 20世纪初,从美国福特汽车公司创立第一条汽车生产流水线以来,大规模的生产流水线一直是现代工业
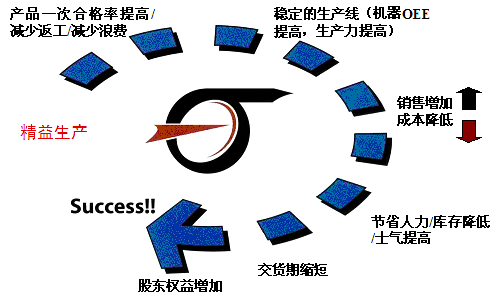
生产的主要特征。大规模生产方式是以标准化、大批量生产来降低生产成本,提高生产效率的。这种方式适应了美国当时的国情,汽车生产流水线的产生,一举把汽车从少数富翁的奢侈品变成了大众化的交通工具,美国汽车工业也由此迅速成长为美国的一大支柱产业,并带动和促进了包括钢铁、玻璃、橡胶、机电以至交通服务业等在内的一大批产业的发展。大规模流水生产在生产技术以及生产管理史上具有极为重要的意义。但是第二次世界大战以后,社会进入了一个市场需求向多样化发展的新阶段,相应地要求工业生产向多品种、小批量的方向发展,单品种、大批量的流水生产方式的弱点就日渐明显了。为了顺应这样的时代要求,由日本丰田汽车公司首创的精益生产,作为多品种、小批量混合生产条件下的高质量、低消耗进行生产的方式在实践中摸索、创造出来了。 1950年,日本的丰田英二考察了美国底持律的福特公司的轿车厂。当时这个厂每天能生产7000辆轿车,比日本丰田公司一年的产量还要多。但丰田在他的考察报告中却写道:“那里的生产体制还有改进的可能”。 战后的日本经济萧条,缺少资金和外汇。怎样建立日本的汽车工业?照搬美国的大量生产方式,还是按照日本的国情,另谋出路,丰田选择了后者。日本的社会文化背景与美国是大不相同的,日本的家族观念、服从纪律和团队精神是美国人所没有的,日本没有美国那么多的外籍工人,也没有美国的生活方式所形成的自由散漫和个人主义的泛滥。日本的经济和技术基础也与美国相距甚远。日本当时没有可能全面引进美国成套设备来生产汽车,而且日本当时所期望的生产量仅为美国的几十分之一。“规模经济”法则在这里面临着考验。 丰田英二和他的伙伴大野耐一进行了一系列的探索和实验,根据日本的国情,提出了解决问题的方法。经过30多年的努力,终于形成了完整的丰田生产方式,使日本的汽车工业超过了美国,产量达到了1300万辆,占世界汽车总量的30%以上。 制造、电子、计算机、飞机制造等工业中。丰田生产方式是日本工业竞争战略的重要组成部分,它反映了日本在重复性生产过程中的管理思想。丰田生产方式的指导思想是,通过生产过程整体优化,改进技术,理顺物流,杜绝超量生产,消除无效劳动与浪费,有效利用资源,降低成本,改善质量,达到用最少的投入实现****产出的目的。 日本企业在国际市场上的成功,引起西方企业界的浓厚兴趣,西方企业家认为,日本在生产中所采用的方式是其在世界市场上竞争的基础。20世纪80年代以来,西方一些国家很重视对丰田生产方式的研究,并将其应用于生产管理。 二、核心思想: 1、追求零库存: 精益生产是一种追求无库存生产,或使库存达到极小的生产系统,为此而开发了包括“看板”在内的一系列具体方式,并逐渐形成了一套独具特色的生产经营体系。 2、追求快速反应,即快速应对市场的变化: 为了快速应对市场的变化,精益生产者开发出了细胞生产、固定变动生产等布局及生产编程方法。 3、企业内外环境的和谐统一 : 精益生产方式成功的关键是把企业的内部活动和外部的市场(顾客)需求和谐地统一于企业的发展目标。 4、人本位主义: 精益生产强调人力资源的重要性,把员工的智慧和创造力视为企业的宝贵财富和未来发展的原动力a、充分尊重员工;b、重视培训;c、共同协作。 5、库存是“祸根” : 高库存是大量生产方式的特征之一。由于设备运行的不稳定、工序安排的不合理、较高的废品率和生产的不均衡等原因,常常出现供货不及时的现象,库存被看作是必不可少的“缓冲剂”。但精益生产则认为库存是企业的“祸害”,其主要理由是:1、库存提高了经营的成本;2、库存掩盖了企业的问题。 效果 精益生产主要研究时间和效率 , 精益生产注重提升系统的稳定性 ,50多年来精益生产的成功案例已证实:: ·精益生产让生产时间减少 90%; ·精益生产让库存减少 90%; ·精益生产使生产效率提高 60%; ·精益生产使市场缺陷减少 50%; ·精益生产让废品率降低 50% ; ·精益生产让安全指数提升 50%。 制造业经常面临的问题 ·产能不够无法满足市场需求 ·不能按时按量交货 ·人员效率低下 ·库存太高,积压资金 ·质量无法满足客户要求 >>点此返回 |